In the fast-paced world of paper production, maintaining seamless operations can be a daunting task. With machines running for extended hours, any downtime can lead to significant losses in productivity and revenue. One of the most effective strategies that companies have adopted to mitigate these challenges is Total Productive Maintenance (TPM). This blog post will introduce you to TPM, its principles, and how it can transform your paper production processes.
What is Total Productive Maintenance (TPM)?
Total Productive Maintenance (TPM) is a holistic approach to equipment maintenance that focuses on proactive and preventative measures. The goal is to increase the operational efficiency of machinery, reduce downtime, and improve overall productivity. Firstly introduced in Japan during the 1960s, TPM has evolved into a powerful process in various industries, including paper production.
TPM is built on the idea that everyone in the organization, from management to operators, should be involved in maintaining and improving the effectiveness of equipment. This collaborative effort leads to a culture of continuous improvement, whereby employees feel empowered to contribute to the upkeep of machinery.
The 8 Pillars of TPM
TPM is structured around eight key pillars, each aimed at improving different aspects of equipment management and performance. Here’s a brief overview of these pillars:
1. Autonomous Maintenance: Operators are trained and encouraged to perform maintenance tasks, enabling them to take ownership of their machines. This reduces the dependency on maintenance teams and fosters a sense of responsibility among employees.
2. Planned Maintenance: This pillar focuses on scheduling regular maintenance tasks to prevent unexpected breakdowns. By planning maintenance activities, companies can minimize downtime and extend the life of their machines.
3. Quality Maintenance: Quality maintenance emphasizes the importance of producing defect-free products. By integrating quality checks into the maintenance process, paper mills can ensure that machines are performing optimally and producing high-quality paper.
4. Focused Improvement: Teams work on identifying and addressing the root causes of inefficiencies. By focusing on continuous improvement, companies can streamline their processes and enhance productivity.
5. Early Equipment Management: This involves incorporating maintenance considerations into the design and installation of new equipment. By doing so, potential issues can be avoided, promoting smoother operations from the outset.
6. Training and Education: Ensuring that all employees are well-trained in the operation and maintenance of equipment is crucial for success. Ongoing training fosters a culture of learning and helps employees adapt to new technologies.
7. Safety, Health, and Environment: This pillar emphasizes maintaining a safe work environment by regularly inspecting equipment and promoting safe practices. A focus on safety leads to enhanced employee morale and productivity.
8. TPM in Administration: Administrative processes can also benefit from TPM principles. By streamlining support operations and improving communication, organizations can increase overall efficiency.
Benefits of Implementing TPM in Paper Production
Implementing TPM in paper production can yield numerous benefits, such as:
Increased Efficiency
By reducing downtime through planned maintenance and operator-led upkeep, companies can achieve substantial gains in productivity. In paper production, where high-speed machines are the norm, even small increases in efficiency can lead to significant improvements in output.
Enhanced Quality
With a strong focus on quality maintenance, companies can ensure that their production processes yield defect-free paper products. By integrating quality checks into maintenance routines, organizations can catch issues before they escalate, ultimately leading to higher customer satisfaction.
Reduced Costs
While the initial investment in TPM might seem daunting, the long-term savings from reduced downtime, fewer repairs, and lower operational costs can more than offset these expenses. Companies that adopt TPM often experience lower costs per unit of production, making them more competitive in the industry.
Cultivated Workforce
Involving personnel at all levels of the organization in maintenance activities fosters a committed workforce. When employees feel a sense of ownership over their work and are invested in the success of the organization, morale and job satisfaction improve. This reusable knowledge shared among teams creates a sustainable continuous improvement culture.
Extended Equipment Lifespan
By systematically maintaining equipment and addressing potential issues early on, companies can extend the lifespan of their machinery. This not only reduces the need for costly replacements but also ensures consistent production levels over time.
Improved Safety
Focusing on maintenance and safety together contributes to a safer work environment. Regular inspections and preventive measures can identify hazards before they result in accidents. Moreover, promoting safe working practices reduces injury-related downtime and related costs.
Steps to Implement TPM in Paper Production
Transitioning to a TPM approach in your paper production facility involves several steps:
1. Get Management Buy-in
The first step in implementing TPM is securing commitment from upper management. Leadership must understand the long-term benefits of adopting TPM practices and be willing to provide the necessary resources.
2. Assemble a TPM Team
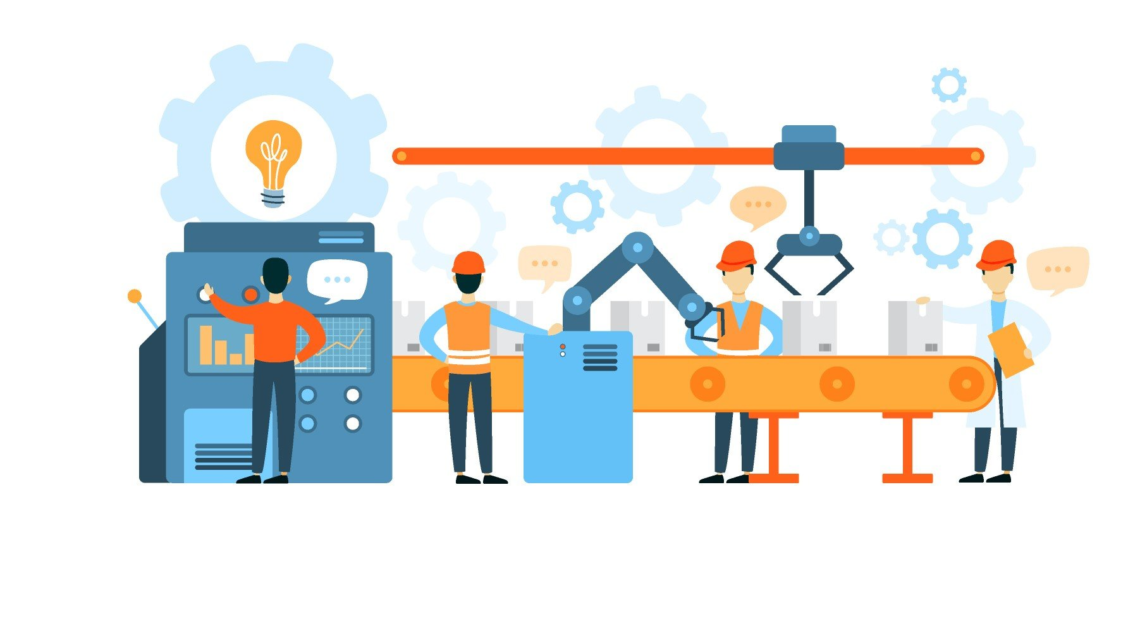
Create a dedicated TPM team that includes representatives from various departments, such as production, maintenance, and quality control. This team’s diverse perspectives will be valuable when developing and implementing TPM strategies.
3. Set Clear Goals
Establish clear and measurable goals for your TPM initiative. These should align with your overall business objectives and should be communicated to all employees.
4. Provide Training
Invest in comprehensive training for all employees involved in the TPM process. By ensuring that everyone is knowledgeable about maintenance practices and equipment operation, you’ll create a stronger foundation for your TPM initiative.
5. Evaluate Current Operations
Conduct an assessment of your current operating procedures to identify areas needing improvement. This evaluation will help you pinpoint specific challenges and establish baseline performance metrics.
6. Develop an Action Plan
Create a detailed action plan to guide the implementation of your TPM initiative. This plan should outline the responsible parties, timelines, and resources needed to achieve your objectives.
7. Monitor Progress
Regularly track the performance of your TPM initiative and make adjustments as needed. Establish key performance indicators (KPIs) to measure progress and evaluate the impact of changes.
8. Foster a Culture of Continuous Improvement
Encourage all employees to contribute to the continuous improvement process. Foster open communication channels and celebrate achievements to maintain momentum.
Conclusion
Total Productive Maintenance (TPM) can have a transformative impact on paper production processes by enhancing equipment reliability, improving quality, and creating a culture of continuous improvement. As companies face growing pressure to stay competitive in a rapidly changing industry, TPM offers a structured approach to maximizing operational efficiency.
While implementing TPM may require an initial investment of time and resources, the long-term benefits such as reduced downtime, enhanced quality, and extended equipment life make it a worthwhile endeavor for any paper production facility. The key is to engage every member of the organization in the pursuit of excellence.
By embracing TPM, you can unlock the full potential of your operations and drive your paper production business toward greater success. Start the journey today, and witness the positive changes unfold as you embrace this powerful maintenance philosophy.
Click here for more information: https://www.ribcon.com/resource-center/total-productive-maintenance/
More Stories
Tax Benefits of Using Virtual Offices
What Are Industrial Cable Glands and How Do They Work?
Benefits of Reviewing PTE Mock Test Results